Olympic Dam Mine
UGL has been providing maintenance services to BHP Billiton (BHP) at their Olympic Dam Mine near Roxby Downs in South Australia for more than 12 years.
Olympic Dam has an extensive underground mine, one of the largest in Australia, with its Northern Mining Area made up of more than 760 km of underground roads and tunnels and a mine depth of around 860m. It has high-quality deposits of copper, gold, uranium and silver, and is known as the fourth largest copper deposit and the single largest uranium deposit in the world.
Details
Location
Olympic DamStatus
CurrentSector
ResourcesExpertise
Client
BHP Billiton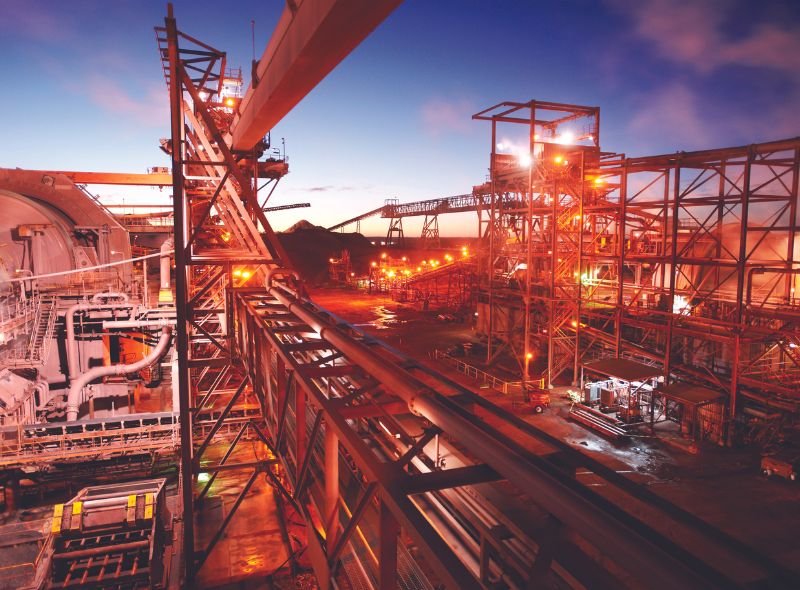
In 2016, UGL achieved ten years and 1 million manhours Lost Time Injury (LTI) free at Olympic Dam – a track record which continues today with zero LTIs onsite since the company implemented its permanent team in 2006.
As an initiative to achieve improvement productivity outcomes and cost savings under the contract. UGL has implemented a continuous improvement framework at Olympic Dam. Under this framework UGL have delivered millions of dollars in cost savings to BHP, with more than 100 improvements documented, across areas which include:
- procurement
- alternative materials selection
- alternative work method
- engineering design to support safety
Project details
The challenge
OD has an extensive underground mine, one of the largest in Australia, with its Northern Mining Area made up of more than 760 km of underground roads and tunnels and a mine depth of around 860m. The underground mine is highly mechanised, with automated rail transportation and underground crushing of ore. The primary method of ore extraction is long-hole open stopping with cemented aggregate fill. Ore is hoisted to the surface, fed into grinding circuits, and then passed to a flotation circuit to produce a copper concentrate. The mine also includes an integrated metallurgical processing plant and expansive open-air tailings storage facilities.
BHP Billiton (BHP) requires its onsite contractors to be focussed on the delivery of safe and fit for purpose solutions, and pro-active in seeking to continually improve the quality of the service provided and identify opportunities to realise value.
Our solution
UGL has worked on projects at Olympic Dam since the late 1980s and has had a full-time presence onsite since 2006. Currently, UGL completes all Mine Major Maintenance contract work and ad-hoc project work both underground and on the surface at Olympic Dam.
UGL works across surface and underground projects and currently has about 150 permanent employees onsite engaged across the areas of asset integrity (civil and mechanical), small modification projects, mine major maintenance and shutdown project work, and maintenance services.
The onsite teams are multi-skilled and consist of experienced rostered personnel to execute a wide variety of maintenance project work using construction management, planning, supervision and trade experience together with the plant and tooling knowledge.
With 12 years of continuous presence onsite working for BHP, UGL has developed an in-depth understanding of the Olympic Dam Mine, and of BHP’s Health, Safety and Environment (HSE) systems and processes and the unique hazards on site. The lessons and learnings accumulated are considered into how UGL continues to deliver services to BHP. The team has a thorough working knowledge of BHP’s uncompromising HSE systems and has a proven safety record working with BHP Billiton at Olympic Dam.
Key outcomes
In 2016, UGL achieved ten years and 1 million manhours Lost Time Injury (LTI) free at Olympic Dam – a track record which continues today with zero LTIs onsite since the company implemented its permanent team in 2006.
UGL has structured its management plan and processes to complement BHP’s site requirements at Olympic Dam, including mapping the BHP safety management systems against the UGL safety management systems. Where the two systems have a comparable system UGL adopts the BHP system to ensure we are ‘talking the same language’ onsite. Where UGL has a system that is not directly comparable UGL integrates this in addition to site requirements. Using this philosophy UGL has achieved a safety management process (SMP) compliance score of 90% which has been used as a benchmark for other contractors onsite.
As an initiative to achieve improvement productivity outcomes and cost savings under the contract. UGL has implemented a continuous improvement framework at Olympic Dam. Under this framework UGL have delivered millions of dollars in cost savings to BHP, with more than 100 improvements documented, across areas which include:
- procurement
- alternative materials selection
- alternative work method
- engineering design to support safety
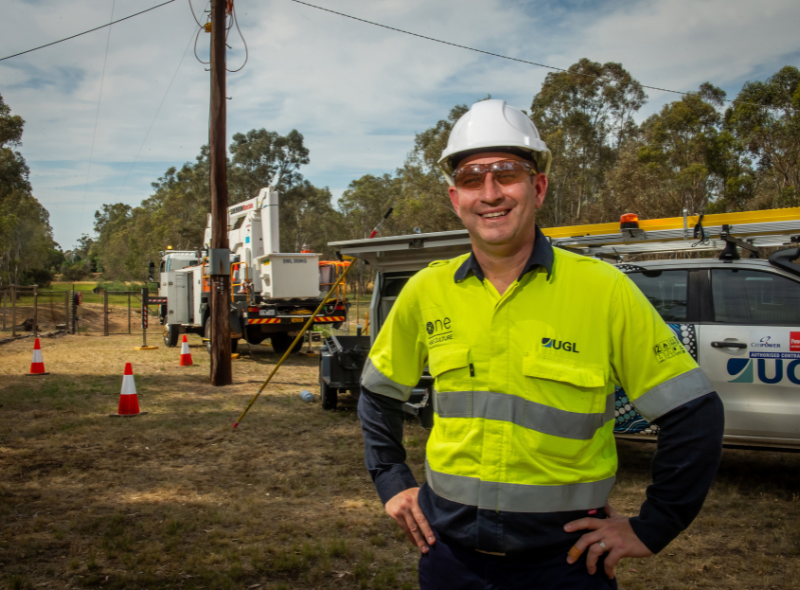
Join our team in Australia
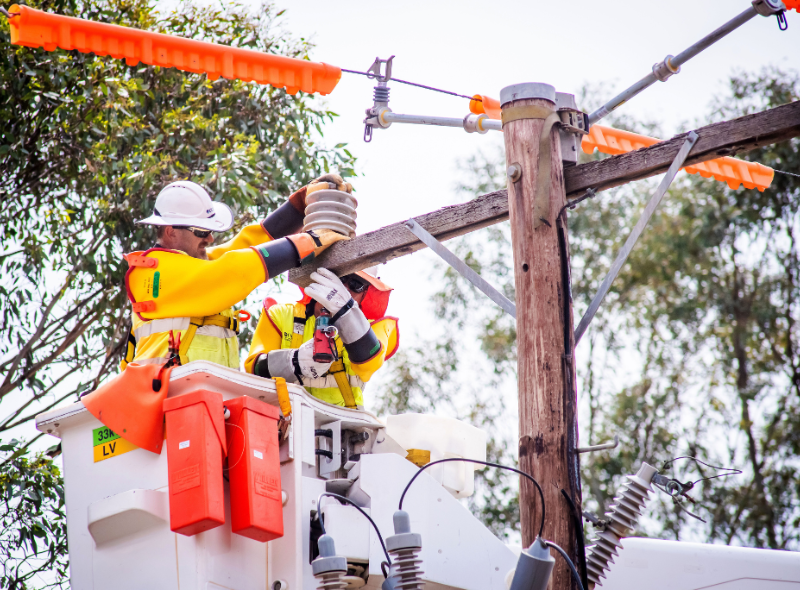
If you’re ready to swap the cool breezes of New Zealand for the warm sunshine of Australia, we’ve got the perfect opportunity for you! Imagine enjoying endless sunny days, exploring vibrant cities, and yes, even developing a taste for Vegemite. Whether you’re seeking new career opportunities, a change of scenery, or just a fresh start, Australia has it all. Embrace the adventure and make the move today—your Aussie dream awaits! 🦘